A73INF Dome type butterfly valve has a logic clear inflating model which supply compressed air to back of seat when the valve close and release compressed air before the valve opening. For abrasive materials like Lithium battery materials, boiler bed sand and limestone, even sticking powder, the inflatable seat can allow solids existing between seat and disc without effecting to sealing. Extra size of solids will be wiped off by the valve construction, sealing are well assured and well protected. Since there is no friction between the disc and the seat when the valve is operated, meanwhile the valve stem is behind the seating ring instead of go through seating ring like traditional inflatable seat butterfly valve, a A73INF Dome type butterfly valve can reach a life of more than three million cycles, providing contact wear compensation even when the valve seat or ball is severely abraded by material. For slurry, bulk powder, particles, irregular solids, adhesive powder, gas and gas powder, the A73INF Dome type butterfly valve ensures the reliability of system operation and increases valve life by magnitude, greatly reducing impact of valve stop or replacement on material production.
Connection | Wafer | Nominal diameter | DN50-DN350 | Max. working pressure | 10Bar | Standard working pressure | Full vacuum to 8bar (According to air supply) | Flange standard | EN1092 PN10/16,ANSI Class150,JIS 10K/16K | Structure length | See drawing | Top flange | ISO 5211 | Seal test | ISO 5208 Category 3, API 598 Table 5 | Temperature range | -40° C to +350° C (Depending on pressure, medium and material | Operation | Pneumatic actuator(DA, SA) | Torque | the torque varies according to different use of medium |
Item | Parts | Material | Standard | Corrosion-resistant and wear-resistant treatment or temperature Remarks | 1 | Valve body | SS304 | ASTM A351 CF8 | Pickling Passivation | SS304+ Tungsten carbide | ASTM A351 CF8+WC | Internal Tungsten carbide coating, external pickling passivation | SS304+Ceramic | ASTM A351 CF8+TC | Internal Ceramic coating, external pickling passivation | SS304+Halar | ASTM A351 CF8+Halar | Internal Halar coating, external pickling passivation | 2 | Valve disc | SS304 | ASTM A351 CF8 | Pickling Passivation | SS304+Halar | ASTM A351 CF8+Halar | Halar coating | SS304+ Tungsten carbide | ASTM A351 CF8+WC | Tungsten carbide coating | SS304+Ceramic | ASTM A351 CF8+TC | Ceramic coating | SS304 +Ni60 | ASTM A351 CF8+Ni60 | Sealing surface with Ni60 weld coating | 3 | Valve seat | Wear-resistant EPDM | EPDM-HT | -20℃ ~120℃ | H160 | H160 | -20℃ ~160℃ | F260 | F260 | -20℃ ~260℃ | Diamond carbon coating SS304 | ASTM A351 CF8+Diamond | -35℃ ~400℃ | 4 | Stem | 431 | SS431 | | 304 | SS304 | | 5 | Packing gland | 304 | ASTM A351 CF8 | Pickling passivation | 6 | Bottom cover | 316 | ASTM A351 CF8M | Pickling passivation | 7 | Packing | RPTFE | RPTFE with 25% carbon fiber reinforced | Temperature to 200℃ | P287 | P287 | Temperature to 300℃ | Graphite | Graphite | Temperature to 400℃ | 8 | Bearing | P287 | P287 | | SS316+high temperature polymer | SS316 | High temperature polymer coating | 9 | Screws | Stainless steel | SS304 | |
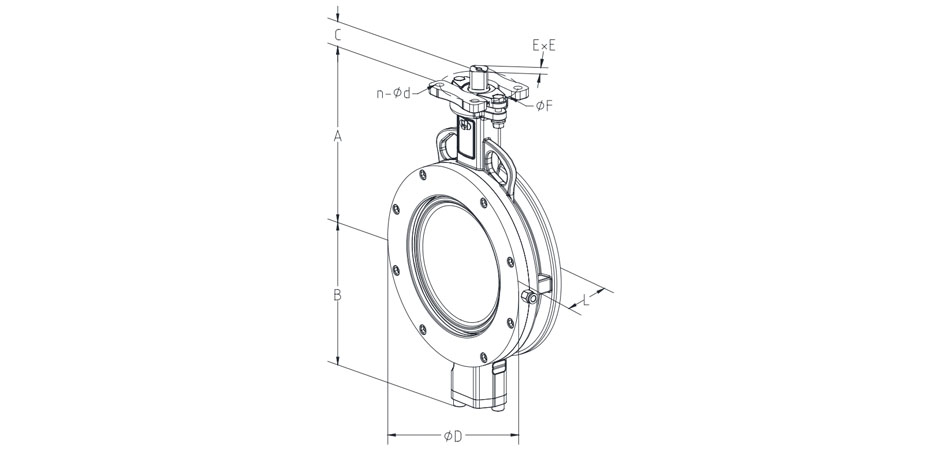
Size | A | B | C | D | E | Top work | L | DN | Inch | 50 | 2" | 126 | 79 | 13.5 | 92 | 11 | F05 | 54 | 65 | 2.5" | 126 | 87 | 13.5 | 105 | 11 | F05 | 56 | 80 | 3" | 145 | 100 | 17.5 | 130 | 11 | F07 | 58 | 100 | 4" | 170 | 124 | 17.5 | 157 | 14 | F07 | 63 | 125 | 5" | 185 | 144 | 17.5 | 186 | 14 | F07 | 65 | 150 | 6" | 203 | 150 | 18.5 | 216 | 17 | F10 | 65 | 200 | 8" | 239 | 186 | 24.5 | 269 | 22 | F10 | 71 | 250 | 10" | 275 | 226 | 24.5 | 324 | 22 | F10 | 77 | 300 | 12" | 307 | 251 | 30 | 380 | 27 | F12 | 83.5 |
Connection | Wafer | Nominal diameter | DN50-DN350 | Max. working pressure | 10Bar | Standard working pressure | Full vacuum to 8bar (According to air supply) | Flange standard | EN1092 PN10/16,ANSI Class150,JIS 10K/16K | Structure length | See drawing | Top flange | ISO 5211 | Seal test | ISO 5208 Category 3, API 598 Table 5 | Temperature range | -40° C to +350° C (Depending on pressure, medium and material | Operation | Pneumatic actuator(DA, SA) | Torque | the torque varies according to different use of medium |
A73INF Dome type butterfly valve has a logic clear inflating model which supply compressed air to back of seat when the valve close and release compressed air before the valve opening. For abrasive materials like Lithium battery materials, boiler bed sand and limestone, even sticking powder, the inflatable seat can allow solids existing between seat and disc without effecting to sealing. Extra size of solids will be wiped off by the valve construction, sealing are well assured and well protected. Since there is no friction between the disc and the seat when the valve is operated, meanwhile the valve stem is behind the seating ring instead of go through seating ring like traditional inflatable seat butterfly valve, a A73INF Dome type butterfly valve can reach a life of more than three million cycles, providing contact wear compensation even when the valve seat or ball is severely abraded by material. For slurry, bulk powder, particles, irregular solids, adhesive powder, gas and gas powder, the A73INF Dome type butterfly valve ensures the reliability of system operation and increases valve life by magnitude, greatly reducing impact of valve stop or replacement on material production.
Item | Parts | Material | Standard | Corrosion-resistant and wear-resistant treatment or temperature Remarks | 1 | Valve body | SS304 | ASTM A351 CF8 | Pickling Passivation | SS304+ Tungsten carbide | ASTM A351 CF8+WC | Internal Tungsten carbide coating, external pickling passivation | SS304+Ceramic | ASTM A351 CF8+TC | Internal Ceramic coating, external pickling passivation | SS304+Halar | ASTM A351 CF8+Halar | Internal Halar coating, external pickling passivation | 2 | Valve disc | SS304 | ASTM A351 CF8 | Pickling Passivation | SS304+Halar | ASTM A351 CF8+Halar | Halar coating | SS304+ Tungsten carbide | ASTM A351 CF8+WC | Tungsten carbide coating | SS304+Ceramic | ASTM A351 CF8+TC | Ceramic coating | SS304 +Ni60 | ASTM A351 CF8+Ni60 | Sealing surface with Ni60 weld coating | 3 | Valve seat | Wear-resistant EPDM | EPDM-HT | -20℃ ~120℃ | H160 | H160 | -20℃ ~160℃ | F260 | F260 | -20℃ ~260℃ | Diamond carbon coating SS304 | ASTM A351 CF8+Diamond | -35℃ ~400℃ | 4 | Stem | 431 | SS431 | | 304 | SS304 | | 5 | Packing gland | 304 | ASTM A351 CF8 | Pickling passivation | 6 | Bottom cover | 316 | ASTM A351 CF8M | Pickling passivation | 7 | Packing | RPTFE | RPTFE with 25% carbon fiber reinforced | Temperature to 200℃ | P287 | P287 | Temperature to 300℃ | Graphite | Graphite | Temperature to 400℃ | 8 | Bearing | P287 | P287 | | SS316+high temperature polymer | SS316 | High temperature polymer coating | 9 | Screws | Stainless steel | SS304 | |
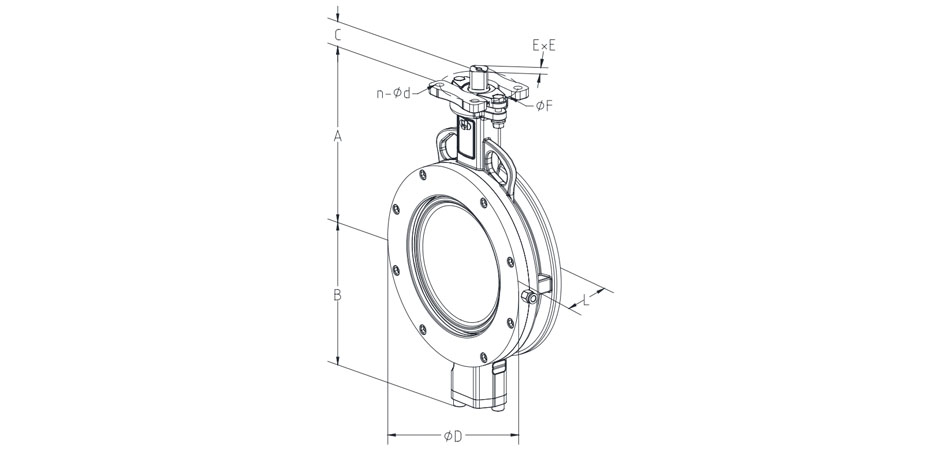
Size | A | B | C | D | E | Top work | L | DN | Inch | 50 | 2" | 126 | 79 | 13.5 | 92 | 11 | F05 | 54 | 65 | 2.5" | 126 | 87 | 13.5 | 105 | 11 | F05 | 56 | 80 | 3" | 145 | 100 | 17.5 | 130 | 11 | F07 | 58 | 100 | 4" | 170 | 124 | 17.5 | 157 | 14 | F07 | 63 | 125 | 5" | 185 | 144 | 17.5 | 186 | 14 | F07 | 65 | 150 | 6" | 203 | 150 | 18.5 | 216 | 17 | F10 | 65 | 200 | 8" | 239 | 186 | 24.5 | 269 | 22 | F10 | 71 | 250 | 10" | 275 | 226 | 24.5 | 324 | 22 | F10 | 77 | 300 | 12" | 307 | 251 | 30 | 380 | 27 | F12 | 83.5 |
|